Case Study: Bugatti Rimac - Practical Problem Solving (PPS)
- Lisa Hynes
- Oct 11, 2024
- 1 min read
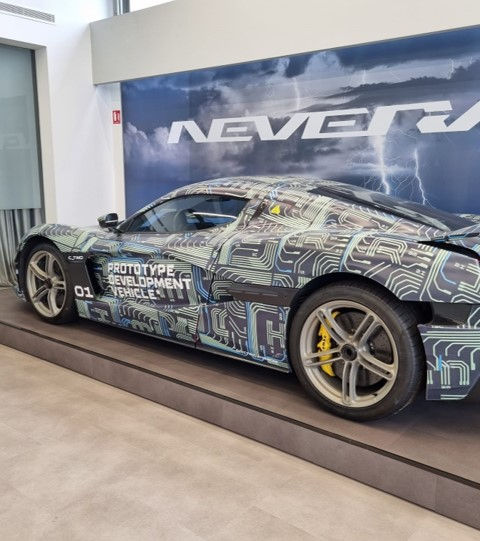
The Problem
Bugatti-Rimac produce some of the finest hyper cars in world and have recruited some of finest engineers from a variety of automotive manufacturers.
The business identified a need to introduce a consistent approach to identifying and resolving issues throughout the entire organisation.
Objectives
To adopt a structured problem solving methodology throughout the entire organisation.
To upskill circa 200 people in their R&D function.
To build a unified and consistent problem solving culture.
To apply structured problem solving to real issues faced in development and production.
To align their internal issue tracking software to their chosen problem solving methodology.
Improvement Activity
A bespoke programme of learning centred around our unique Practical Problem Solving (PPS) model was developed for Bugatti-Rimac.
A team of 20 people were trained as ‘PPS champions’ using a combination of classroom, assignment and virtual coaching methods.
A further group of circa 180 people were given access to PPS eLearning and virtual coaching, support by the previously trained champions.
A collaborative workshop with Bugatti-Rimac and their software provider was delivered to align their issue tracking system to the PPS methodology.
Development of instructional training videos to support the learning journey.
Set up of a Bugatti-Rimac branded learning portal.
Result
Circa 200 people trained within 3 months.
A unified approach to problem solving has been delivered at scale and pace throughout an entire division of an organisation.
PPS methodology has been adopted throughout the organisation.
60 improvement projects have been identified.
Issue tracking software is fully aligned to the PPS methodology.